Project Description
Introduction of Crystallizer copper tube – the round, square, rectangle, non-standard copper molds for steel industry
Crystallizer copper tube for CCM is an accessory used for cast steel continuous casting machine, which is caused by direct casting of molten steel in the mold copper tube.
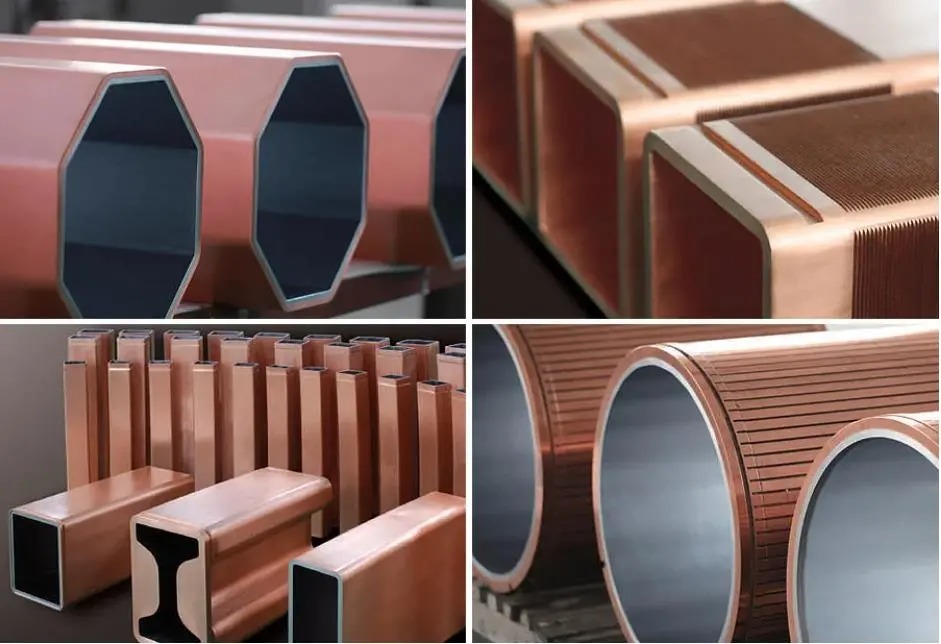
Crystallizer copper tube for steel industry is an essential part that used in any construction. It is created with a good quality of raw materials that produce reliable sources. We provide copper mould tube products based on industry norms and high standards. You might order applications according to your industrial needs. We help you to produce these products on your limited budget to access on your field.
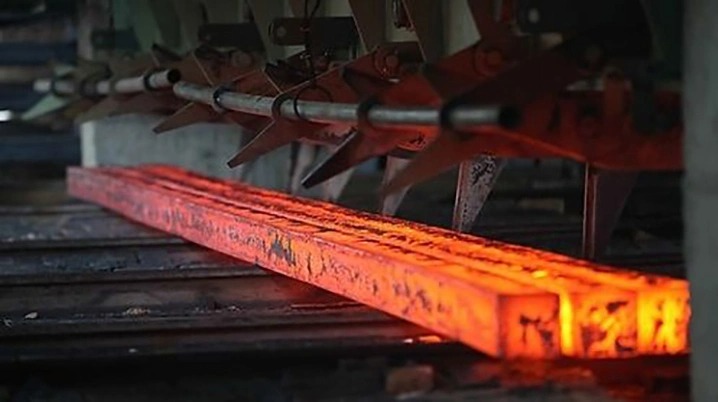
Raw Material of Crystallizer copper tube
To provide mould tubes with optimal physical and mechanical properties to customers’ specifications, mould tube products are supplied of the following materials:
1. Cu-DHP: Normally used for mould tubes section size below 180x180mm and round tubes below Dia.150mm.
2. Cu-Ag: Normally used for mould tube section size above 180x180mm and round tubes above Dia.150mm
3. Cu-Cr-Zr: Normally used for beam blank mould tubes
Specifications of Crystallizer copper tube
We supply all kinds of Copper Mold Tubes of all sizes and dimensions, produced exactly as per the required drawing.
The Sizes for Copper Mould Tubes is enlisted as under:
Production Process of Crystallizer copper tube
MELTING & CASTING — HOT EXTRUSION/FORGING — COLD DRAWING — TAPERING — MACHINING — ELECTROPLATING — MACHINING AFTER ELECTROPLATING — FINAL INSPECTION — PACKING
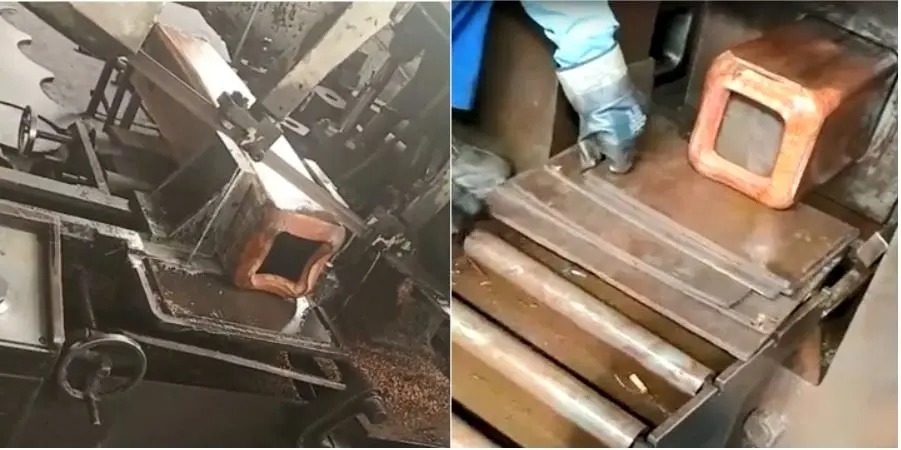
Coating for Crystallizer copper tube
In order to increase the erosion resistance and service life the casting mould tubes, we always dedicated to research special coatings. The mould tubes can be coated with our different types of internal surface coating: Cr, Ni-Co, Ni-Fe, Ni-Co-Cr. The coating thickness recommended by us has been controlled in the best range.
The Advantages of Crystallizer copper tube
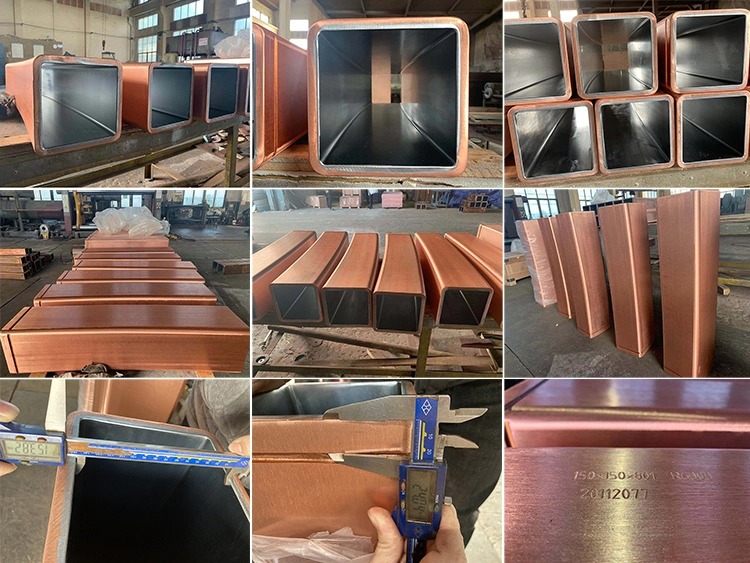
Extra-long service-life is achieved with the special multilayer Ni-Co-Cr coating, which features high micro hardness and optimum binding strength with the copper base. The tubes are designed for maximum heat transfer rate from the meniscus down to the bottom of the tube.
The taper-geometry depends on the steel-grades and casting conditions and is designed with the aim of minimizing the gap between the solidifying shell and the copper tube.
Package for Crystallizer copper tube
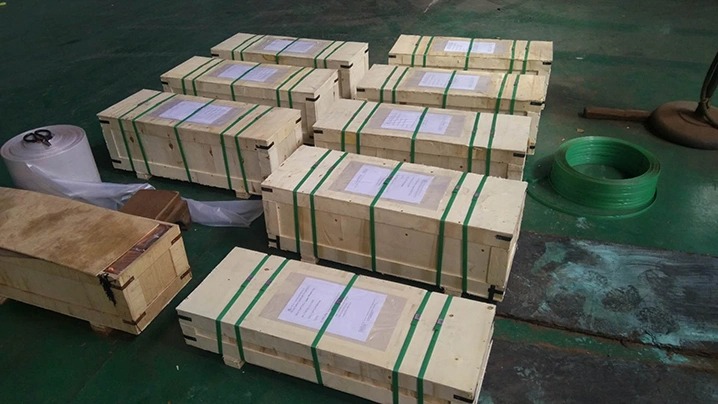